На предприятии «Целинскагрохимсервис» в Ростовской области создана новая система управления линией весового дозирования минеральных удобрений. Система предназначена для автоматического взвешивания и дозирования с высокой точностью, фасовки сыпучих материалов в мешки разного объема, в том числе большие мешки от 500 до 1 200 кг.
Необходимость модернизации
Прежняя линия весового дозирования эксплуатировалась не так долго – около 5 лет, но все это время возникали неполадки в ее работе: нарушалась точность дозирования (пересыпы и недосыпы материала), сбои в работе средств автоматизации.
При выходе из строя и необходимости замены контроллера, датчиков, весовых устройств и пр. возникали проблемы с их приобретением.
Из-за низкой информативности прежней системы управления много сил и средств тратилось на поиск неисправностей и их устранение.
При настройке системы на другой вес приходилось прибегать к неудобному перепрограммированию весового инструмента. Кроме прочего, отсутствовал автоматизированный учет готовой продукции.
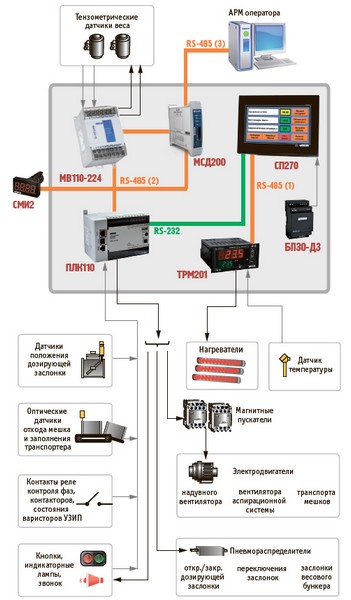
Все это послужило причинами модернизации линии весового дозирования сыпучих материалов. Одним из основных требований заказчика к новой системе управления было применение легкодоступных и заменяемых средств автоматизации отечественного производства.
Технологический цикл весового дозирования
Вес материала измеряется тремя тензометрическими датчиками. При наборе требуемой массы дозирующая заслонка регулирует точность досыпки материала. Положение заслонки контролируют два датчика: один датчик – закрытое положение, другой – среднее.
После установки мешка на патрубок по команде оператора осуществляется раздув мешка воздухом и его загрузка материалом через заслонку. Одновременно с этим работает аспирация, которая включается с задержкой по времени. После заполнения мешок перемещается транспортером. Освободившееся место контролируется оптическим датчиком. При заполнении транспортера мешками срабатывает датчик положения аналогичного типа.
Аппаратные средства управления
Основные средства автоматизации размещены в щите, находящемся в закрытом помещении.
Систему управления образуют приборы ОВЕН (рис. 1):
- программируемый логический контроллер ПЛК110-220.32;
- модуль ввода сигналов тензодатчиков МВ110-224.1ТД;
- сенсорная панель оператора СП270;
- модуль сбора данных МСД200; » светодиодный индикатор СМИ2.
В качестве основного управляющего устройства используется контроллер ПЛК110 с требуемым количеством дискретных входов/выходов и интерфейсов связи. Программа управления ПЛК110 обеспечивает выполнение всего технологического цикла: загрузку бункера, раздув и заполнение мешка, его перемещение. Для удобного завершения работы предусмотрен специальный режим управления транспортером.
Один из алгоритмов, созданных на ПЛК, позволяет повысить точность дозирования за счет непрерывного контроля массы пустого бункера. Программно удалось отстроиться от ряда факторов, влияющих на точность дозирования: налипания материала на стенки бункера, вибрации подающего транспортера, вентилятора и др.
На рабочем месте оператора линии установлен выносной пульт управления с кнопками и компактным светодиодным индикатором СМИ2. Индикатор СМИ2 служит удобным средством отображения оперативной информации, на него выводятся данные в текстовом и числовом формате: режим работы, выполняемая операция, масса материала в весовом бункере, состояние системы и др.
Режимы работы АСУ
Система имеет три основных режима работы:
- автоматический;
- ручной (выполнение отдельных операций технологического цикла);
- режим наладки (для пусконаладочных работ и настройки оборудования).
Повысить гибкость управления и эффективность работы линии удалось за счет функции досрочного завершения любой операции, а также повторного раздува мешка по сигналу оператора. Кроме того, в ручном режиме управления реализована функция досыпки, которой удобно пользоваться при перестройке системы на материал с другой насыпной плотностью.
Постоянно работающая самодиагностика системы позволяет выявлять различные нештатные ситуации.
При аварии включается световая и звуковая сигнализация. В случае выявления критического события происходит отключение всех электроприводов и перевод заслонок в закрытое положение.
Графический интерфейс оператора
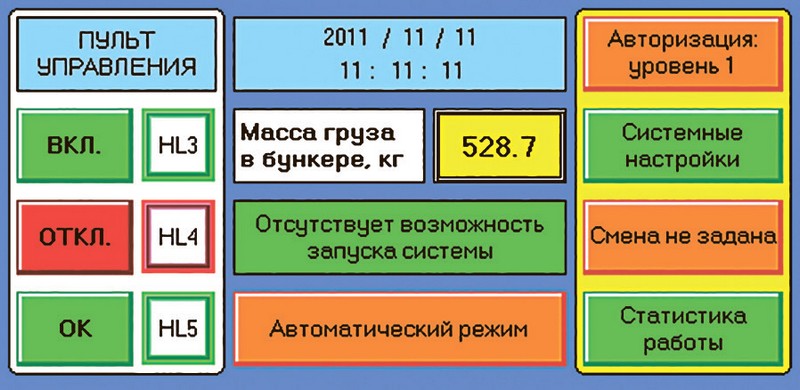
Управление линией весового дозирования сыпучих материалов качественно улучшено за счет применения HMI-средств: светодиодного индикатора СМИ2 и панели СП270.
Для СП270 разработан простой, интуитивно понятный графический интерфейс оператора, который позволяет легко настраивать систему на требуемую массу и точность дозирования материала, менять параметры работы установки, оперативно отслеживать состояние системы и пр.
Для проведения технологических работ обслуживающему персоналу необходимо пройти авторизацию. В зависимости от уровня доступа созданы разграничения: ОПЕРАТОР, ТЕХНОЛОГ, НАЛАДЧИК. Последний обладает полным доступом к настройкам и управлению системы.
Разработанные экраны графического интерфейса панели СП270 в значительной степени облегчают настройку и отладку системы управления. Кнопки и индикаторные лампы в левой области главного экрана панели представляют собой графический пульт управления (рис. 2). Их функциональность аналогична кнопкам и лампам выносного пульта управления.
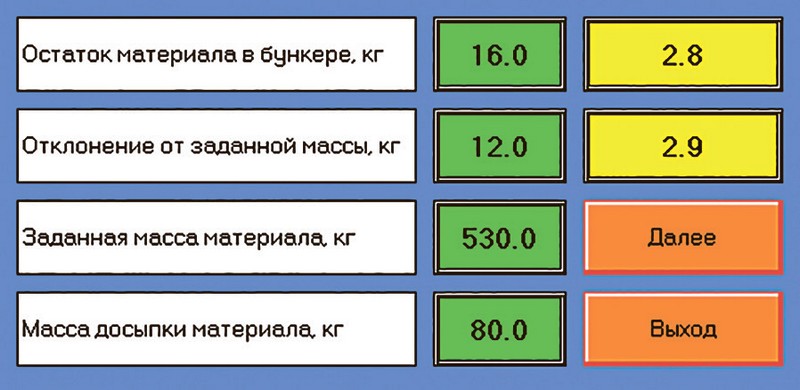
Контроллер реализует самодиагностику системы управления и выявляет 12 возможных аварийных событий. Критические события, при которых дальнейшая эксплуатация системы невозможна, заносятся в ПЗУ панели СП270. Их просмотр возможен на экране «Аварийные события».
Задание требуемой массы и точности дозирования осуществляется на экране «Настройки 1 весового инструмента» (рис. 3). Для более детальной настройки весового инструмента предусмотрен экран «Настройки 2 весового инструмента» (рис. 4).
Для контроля процесса фасовки информация по последним 50 мешкам заносится в ОЗУ панели СП270 и отображается на экране «Статистика работы».
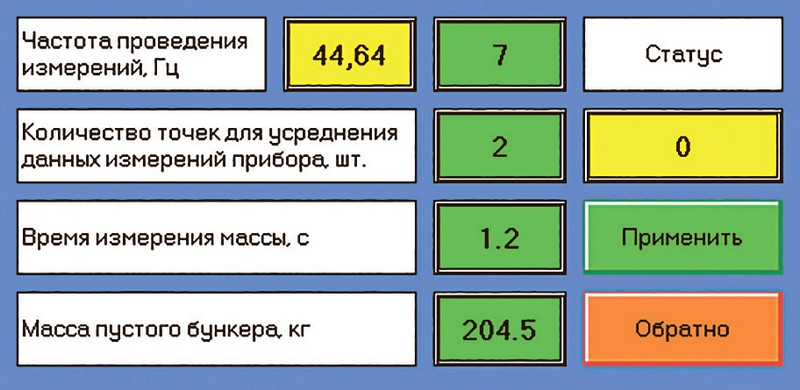
Дополнительный функционал
Статистические данные работы линии записываются модулем МСД200 в файл на SD-карту памяти. По запросу эта информация передается на удаленный ПК и загружается в базу данных программы 1C для последующей обработки и анализа.
Разработана локальная система обогревом щита управления с индикацией внутренней температуры воздуха на базе измерителя-регулятора ОВЕН ТРМ201. Доступ к настройкам терморегулятора ограничен (кнопки ТРМ201 заблокированы) и возможен только через отдельный экран графического интерфейса. Кроме установки требуемой температуры, возможен переход на ручной режим управления, а также скрытая возможность блокировки/разблокировки кнопок ТРМ201.
Для улучшения условий работы в зимнее время производится подогрев пола площадки оператора. Регулирование температуры нагрева пола осуществляется вручную (без обратной связи) с помощью твердотельного реле HD-2544.VA.
Результаты модернизации АСУ
Разработанная АСУ линией весового дозирования сыпучих материалов на предприятии «Целинскагрохимсервис» позволила улучшить эргономичность рабочего места оператора, повысить информативность и гибкость системы управления, облегчить перенастройку системы, снизить погрешность дозирования и автоматизировать учет фасованных мешков.
Эксплуатация линии дозирования в течение года подтвердила высокую надежность и стабильность работы системы управления. Даже в условиях низких температур (ниже –15 °С), высокой влажности и химически агрессивной среды система работоспособна и поддерживает высокую точность дозирования материала в пределах ±1 кг.
Связаться с автором проекта можно по телефону: 8 (928) 769-38-93 или по адресу: sea007@rambler.ru