С компанией ОВЕН я познакомился несколько лет назад – на выставке ПТА. На тот момент передо мной стояла задача восстановить регулирование температуры на трёх резиносмесителях. Сразу оговорюсь, что наше предприятие ООО ПКФ «Астрахим» – немолодое, на нем до последнего времени продолжали работать релейные схемы и приборы выпуска до 80-х годов. Такая ситуация сложилась не только на нашем предприятии – по всей России, поэтому и захотелось поделиться личным опытом по выбору средств автоматизации и последующей работы с ними.
Первым прибором ОВЕН стал одноканальный регулятор ТРМ201 с интерфейсом RS-485. Меня привлекли, во-первых, его функциональность – ровно то, что требовалось для управления оборудованием и, во-вторых, стоимость и простота настройки. Забегая вперед, могу сказать, что приборы показали себя с надежной стороны и по сей день исправно работают. Этот опыт стал началом широкого внедрения приборов ОВЕН. Регулярно просматривая журнал «Автоматизация и производство» и посещая сайт компании www.owen.ru, мы искали решения, подходящие для нашего производства. Результатом стало внедрение тридцати восьми приборов ТРМ138 для регулирования температуры плит вулканизационных прессов. Затем на линии, состоящей из 10 прессов (фото 1), были заменены старые релейные схемы на контроллеры ПЛК100, «обвязка» остальных прессов – вопрос времени.
В формовом цехе предприятия находятся 38 вулканизационных прессов, 2 экструдера и 3 экспериментальных пресса с вакуумными камерами. Инженерам ООО ПКФ «Астрахим» предстояло решить задачу регулировки температуры пяти плит пресса с точностью 4 0 С и передачи данных на компьютер. На все прессы установили восьмиканальные регуляторы ОВЕН ТРМ138 с интерфейсом RS-485. Они идеально подошли для решения этой задачи – с их помощью регулируется температура с необходимой точностью. Вдобавок были установлены три модуля ввода ОВЕН МВА8 для сбора информации о длительности процесса вулканизации и о числе циклов работы пресса.
Удобство и надёжность использующихся приборов настолько вдохновили наших сотрудников, что было решено пересмотреть схему управления процессом формовки резиновых заготовок. Программируемый контроллер ОВЕН ПЛК100 в этом решении полностью заменил сложную устаревшую релейную схему управления. К нему подключили все имеющиеся датчики и силовое оборудование. Структурная схема линии из 16-ти прессов показана на схеме (рис. 1). Для удобства работы прессовщика была добавлена панель оператора ОВЕН СМИ1, которая отображает данные о времени вулканизации.
Хотелось бы отметить, что, на наш взгляд, компания ОВЕН верно выбрала среду разработки CoDeSys для своих контроллеров, поскольку она позволяет проектировать схемы автоматизации любому технически грамотному специалисту, начиная от электрика и заканчивая высококвалифицированным программистом.
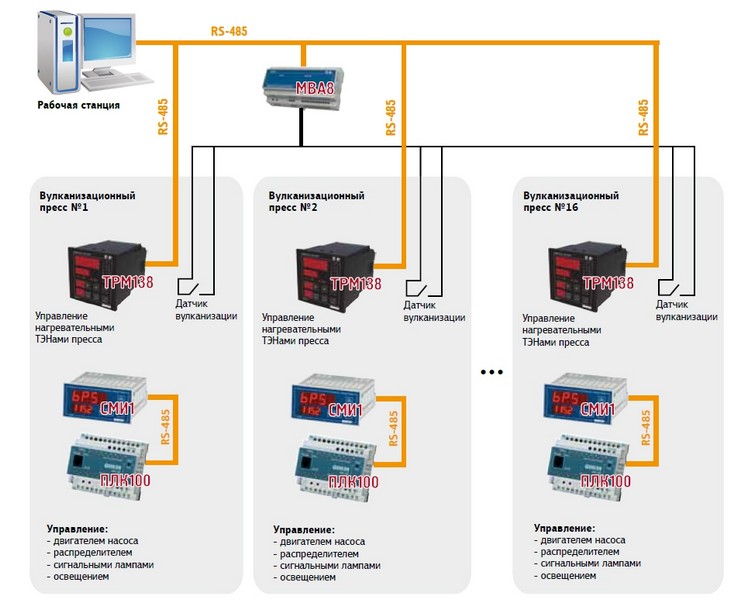
Для наблюдения за работой прессов и архивирования параметров процесса была разработана программа «Лаура. Контроль». Возможности программы довольно обширны, она не только отображает и архивирует параметры, такие как температура пяти плит пресса, длительность, количество циклов, но и выявляет, и оповещает о нарушениях в работе оборудования и авариях. Мастер формовочного участка постоянно находится в курсе событий, протекающих на прессах. Сейчас ведётся работа по оснащению пресса быстродействующим модулем ОВЕН МВ110-8AC и датчиком давления. Это позволит регулировать давление в гидросистеме пресса без использования стрелочного двухпозиционного манометра.
Подвергнется модернизации и способ мониторинга работы прессов. Контроллер ПЛК100 будет опрашивать ТРМ138 и передавать данные по Ethernet на рабочую станцию. С помощью технологии «Клиент-сервер» данные будут не только отображаться у мастера смены, но и передаваться на другие участки и в центральную заводскую лабораторию для формирования паспорта на выпущенную партию пробок.
В подготовительном цехе для просмотра и архивирования температуры на трех резиносмесителях работают три регулятора ТРМ201. На рабочую станцию установлена программа СТАТ-8 для архивирования температуры.
Использование приборов ОВЕН на предприятии «Астрахим» значительно сократило брак продукции. Срок окупаемости выполненных работ составил два года. Прессы стали работать надёжней, не требуя кропотливого ремонта, приводящего к простою оборудования.