На хлебокомбинате в г. Рудня Смоленской области длительное время эксплуатируется комплекс для выпечки хлебобулочных изделий производства DAUB (Нидерланды). Комплекс состоит из котла, оснащенного блочной горелкой ELCO, и двух камер для выпечки, соединенных с котлом системой трубопроводов (рис. 1). Теплоносителем служит минеральное или синтетическое масло. В зависимости от вида выпекаемой продукции масло нагревается до 270 – 300 °С и подается в камеры выпечки циркуляционным насосом Allweiler. Температура в камерах поддерживается в соответствии с установленной программой управления путем изменения количества подаваемого теплоносителя.
Техническое несовершенство и физический износ штатной системы управления котла привели к аварийной ситуации: загустевшее масло закупорило теплообменные трубы, нарушив его циркуляцию. Автоматика не среагировала, произошло возгорание. В результате оборудование вышло из строя на длительный срок. Нанесенный ущерб убедил владельца предприятия провести модернизацию системы управления для предотвращения подобных проблем в будущем.
Система управления
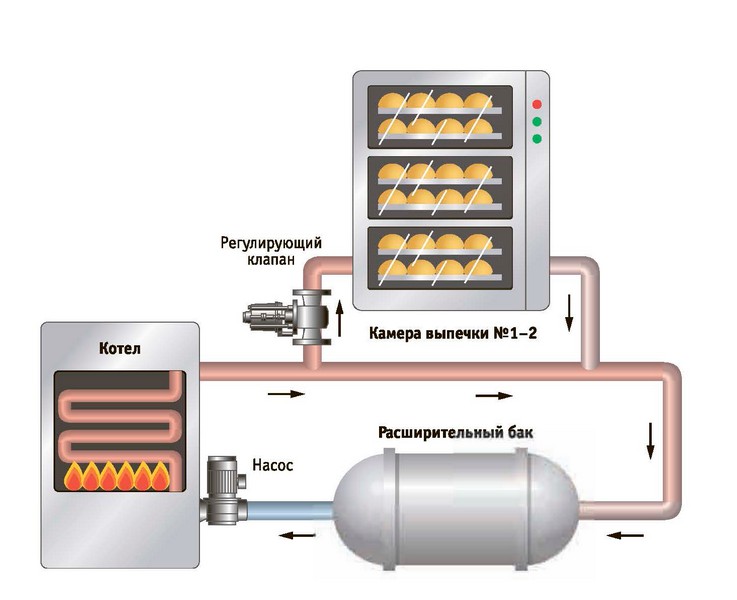
Разработку новой системы управления, ее монтаж и пуско-наладку выполнила компания ИНВЕРТ-СЕРВИС. В соответствии с нормативными требованиями система обеспечивает контроль:
- давления теплоносителя в напорном трубопроводе;
- уровня теплоносителя в расширительном баке;
- расхода теплоносителя;
- температуры теплоносителя в прямом и обратном трубопроводах;
- температуры дымовых газов.
В качестве основного управляющего элемента используется свободно программируемый контроллер ОВЕН ПЛК63 (рис. 2). Выбор данного контроллера обоснован наличием совместимых с оборудованием интерфейсов: аналоговых входов с возможностью подключения датчиков давления и температуры, дискретных выходов для управления насосом и горелкой. Кроме этого, все необходимые интерфейсы и точки ввода/ вывода сосредоточены на одном ПЛК, т.е. дополнительные модули расширения не потребовались. Для визуализации режимов работы используется сенсорная панель ОВЕН СП.
Элементы измерительной системы
Основная технологическая проблема была связана со свойствами теплоносителя: высокая рабочая температура (до 300 °С), склонность к загустеванию и налипанию, а также крайне низкая электропроводность. Все элементы измерительной системы подбирались с учетом этих особенностей.
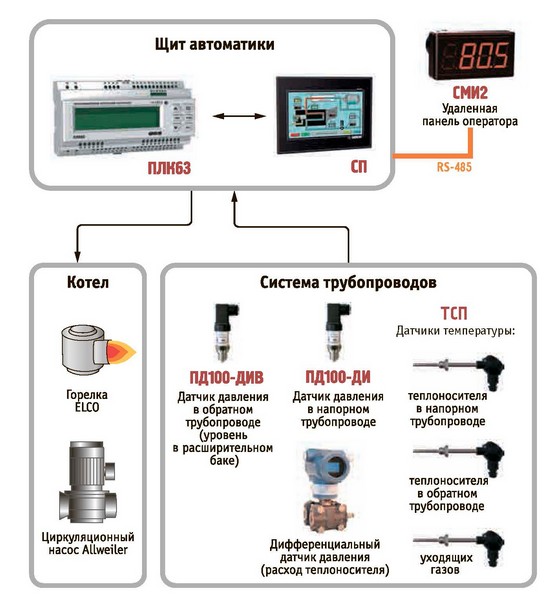
Датчик давления ОВЕН ПД100-ДИ с открытым сенсором был выбран по причине высокой точности измерений, стабильной работы и главное – возможности его очистки от отложений теплоносителя в напорном трубопроводе.
С измерением уровня теплоносителя в расширительном баке также возникали проблемы: из-за низкой электропроводности масла кондуктивные датчики уровня не реагировали даже при выборе максимально низкого порога срабатывания, поплавковые датчики не выдерживали высокой температуры, ультразвуковые датчики уровня оказались слишком дороги. В результате измерять уровень теплоносителя в баке стали косвенным методом – в соответствии с давлением в обратном трубопроводе. Для этого перед насосом был установлен датчик ОВЕН ПД100-ДИВ с открытым сенсором. Опыт показал правильность выбранного метода и удовлетворительную точность измерений.
Косвенный способ измерения – с помощью дифференциального датчика давления – применили также и для учета объема теплоносителя, протекающего через котел. Добиться снижения температуры теплоносителя, которая может достигать 300 °С, стало возможным благодаря подключению датчиков к рабочим точкам посредством длинных медных импульсных трубок. Такое подключение позволяет снизить температуру с 300 до 100 °С.
Температура теплоносителя в прямом и обратном трубопроводах, а также температура дымовых газов в газоходе измеряется платиновыми термопреобразователями сопротивления ТСП.
Работа комплекса
Первым включается циркуляционный насос. Автоматика контролирует давление, наличие протока теплоносителя через котел и отсутствие падения уровня в расширительном баке. При отклонении любого параметра от заданных величин процесс будет немедленно прекращен. Если в течение установленного времени все параметры остаются в норме, запускается циркуляция теплоносителя, затем включается одноступенчатая немодулируемая горелка с двухпозиционным регулированием, и начинается разогрев масла. Непрерывно ведется контроль работы оборудования. На рис. 3 показан основной экран панели управления.
Аварийное отключение котла с выводом на панель предупреждающего сообщения происходит в случаях:
- частичной или полной закупорки теплообменных труб (рост давления теплоносителя в напорном трубопроводе за насосом или снижение перепада давления на сужающемся участке, или увеличение температуры газов);
- утечки теплоносителя (снижение давления теплоносителя в обратном трубопроводе);
- неисправности циркуляционного насоса (снижение давления теплоносителя в напорном трубопроводе или снижение перепада давления);
- перегрева теплоносителя;
- неисправности горелки.
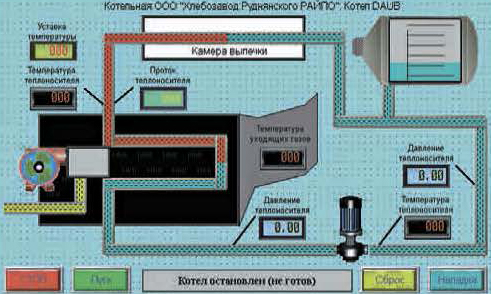
Помимо технологических параметров автоматика контролирует исправность всех датчиков и в случае выхода из строя одного из них также останавливает котел. Для диагностики неисправностей и иных целей возможно отключение контроля любого технологического параметра. Доступ к уставкам аварийных параметров защищен паролем. На рис. 4 показан экран наладки панели управления.
Штатное выключение комплекса происходит в обратном порядке: по команде оператора горелка отключается, а циркуляция теплоносителя продолжается вплоть до его охлаждения. В связи с тем, что котел и камеры выпечки установлены в разных помещениях, для удобства оператора на панели управления камерами смонтирован мини-индикатор ОВЕН СМИ2 – для отображения температуры теплоносителя на выходе из котла и различных аварийных сообщений. Панель подключена к основному блоку автоматики котла по RS-485.
Система автоматики успешно прошла пусконаладочные испытания, находится в эксплуатации и показала высокую эффективность.
Вопросы и заявки можно направлять по почте: sorokin@elec.ru или по тел.: +7 (920) 305-2694